Most common Airport Passenger Boarding Bridges
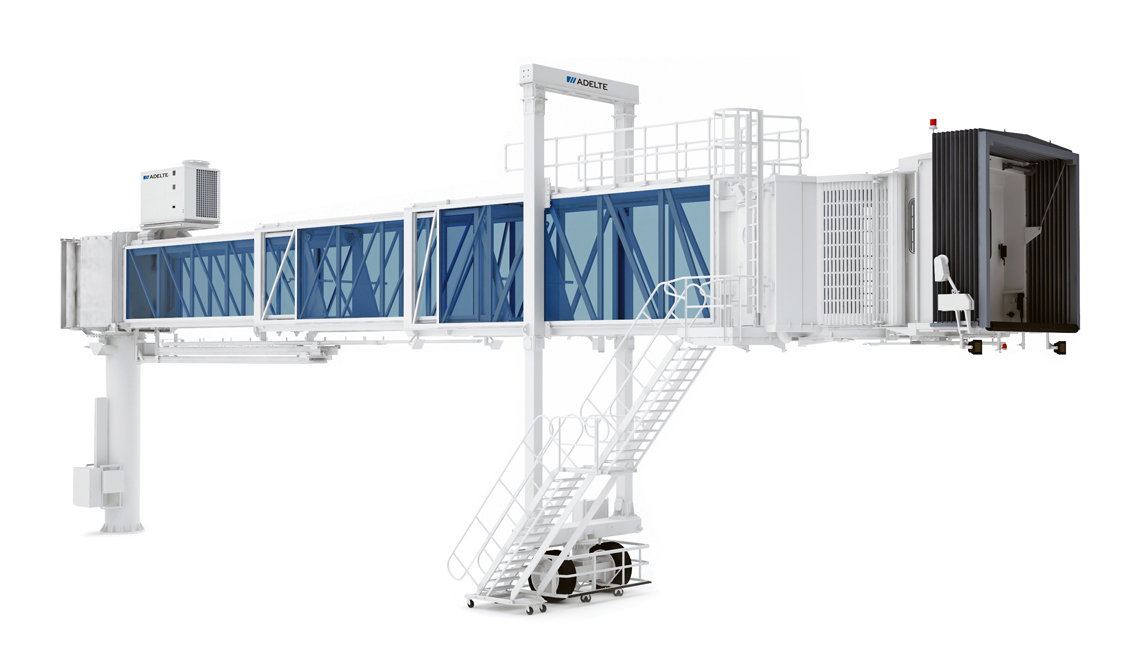
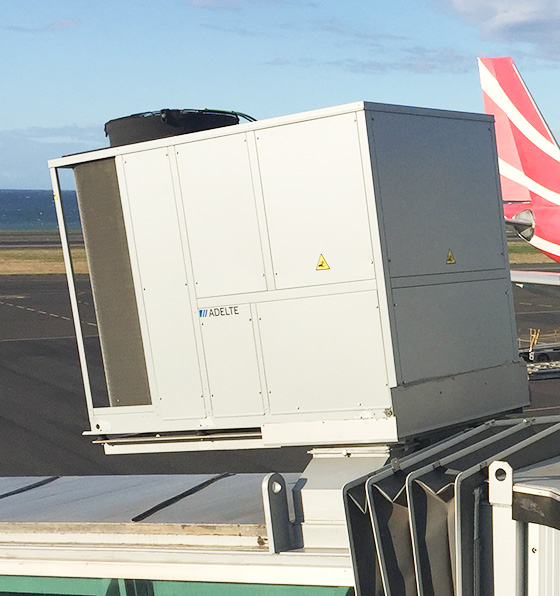
Rooftop
Designed to perfectly meet the thermal needs inside the PBB in all climate conditions. It is equipped with internal air ducting system to distribute the conditioned air throughout the PBB.
- Cooling capacity of 30,5kW
- R-410A
- Specially designed for Passenger Boarding Bridges
- Equipped with 2 impulsion outlets and 1 return inlet directly connected to the PBB
- Energy Efficiency Ratio (EER) of 2,9
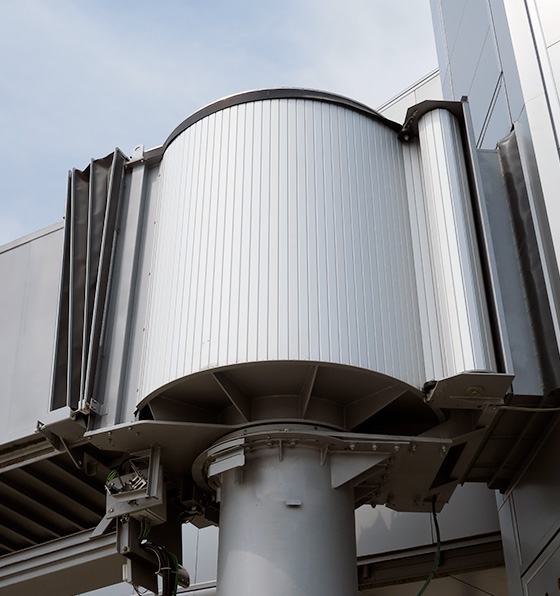
Rotunda
The roomy and bright inner space improves passenger comfort and flow. The specific design of the blinds, with prestressed springs and without the need for a roller shutter chain eliminates noise during rotation.
- Water proof aluminum slats for noise reduction for extended life
- Synchronized slat rotation system without chain/gear (maintenance free)
- Heavy duty low friction slewing ring
- Rotation up to ±90º
- 1 Rotation limit switch and 2 proximity sensors
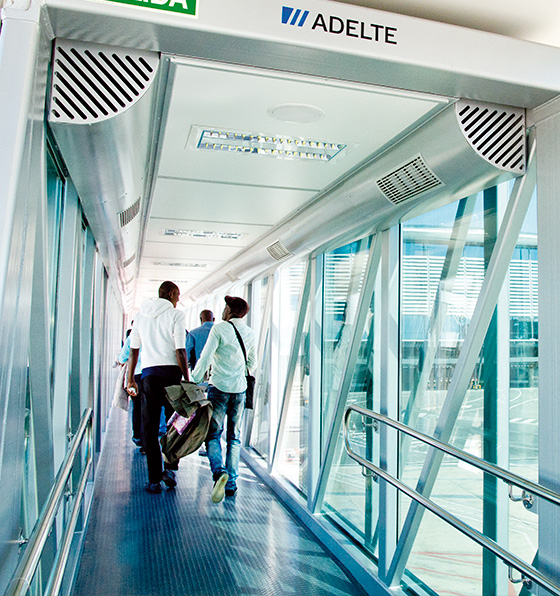
Telescopic Tunnels
The structure, made of high quality steel, has undergone a category C5-M paint process which is specifically developed for harsh environments.
- High efficiency air conditioning ducting system (optional)
- Side metal panels with great thermal insulation, optional with double glazed windows
- Noise insulation for a better boarding experience
- Anti slip flooring, extreme durable and easy to maintain PASS-PORT Gerflor (a wide variety of designs and colors available)
- Quality coating of the steel structures with heavy duty three layer system 320µ d.f.t), guaranteeing five years touch- up free and endurance for the life of the structure (20+ years)
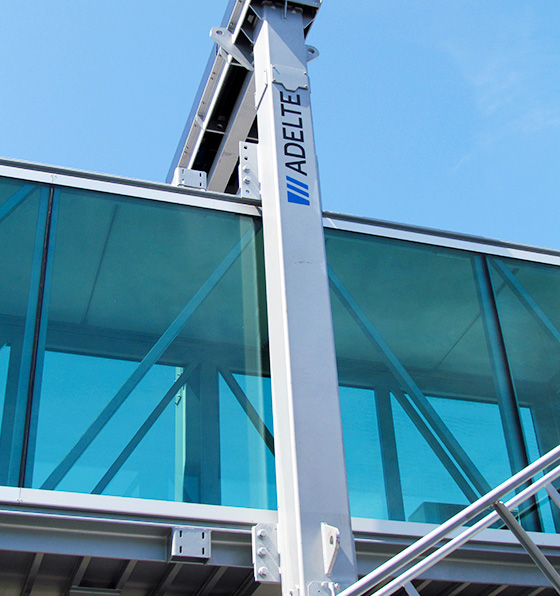
Elevation System
Electromechanical or hydraulic systems are available as standard. Both are equipped with a redundant safety system that ensures the alignment of the lifting columns at all times without the need for electrical detectors.
- Elevation through two simple effect hydraulic cylinders or Synchronized electromechanical elevation with heavy duty bearing system (ACME)
- Oil tank attached to the bogie allowing easy access for inspection and maintenance
- Hydraulic circuit equipped with filters for virtually maintenance free life of the system or Electromechanical safety brakes mechanically activated without power supply
- All standard components are global first class brand products like Siemens, Telemecanique, Vickers or Parker
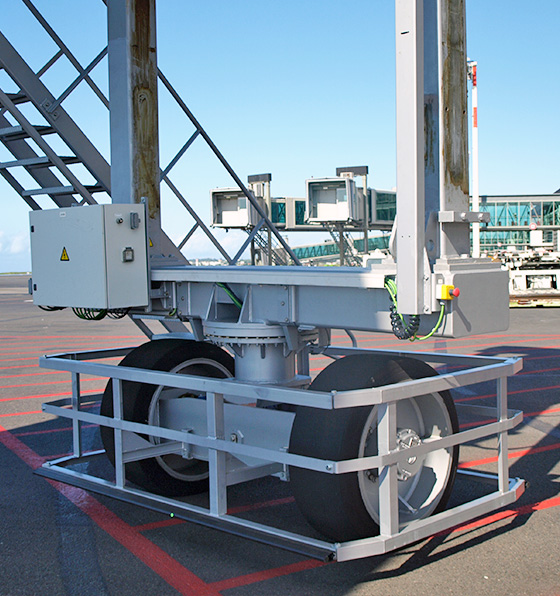
Traction System
This consists of a solid double wheel that is highly resistance to wear, independently controlled by a few variators through the PLC. The advanced design of the bogie allows instant access to any part of the traction system that requires maintenance.
- Equipped with two heavy duty motors
- Bogie rotation monitored by an incremental encoder
- Anti shock system for operators and handling personnel safety and security
- All standard components are global first class brand products like Hohner or Telemecanique
- 2 Proximity sensors
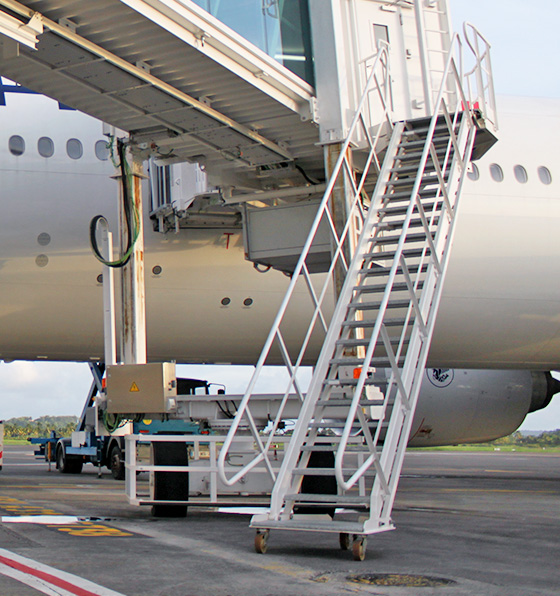
Service Stairs
Stairs with a robust design made from high-quality steel with slip-resistant, self-levelling steps to avoid any risk of the handling operators falling.
- Light and robust design for an easy access to the cabin
- Galvanized or painted steel for long lasting
- Anti-slip steps and safety handrails installed at both sides
- Strong heavy duty spinning wheels
- Sun resistant weather proof cover (optional)
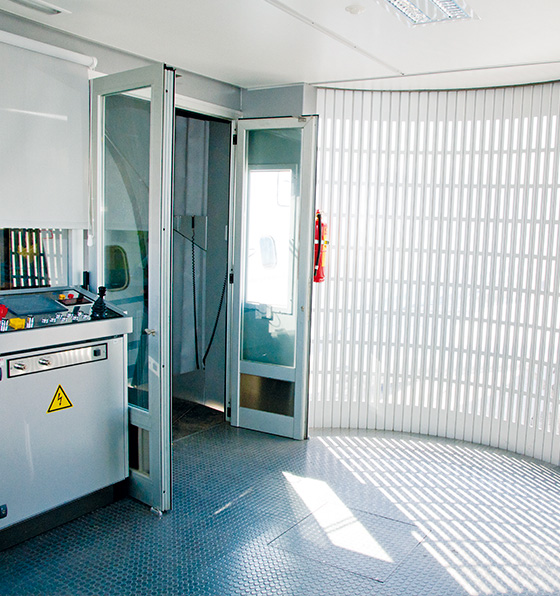
Cabin
The inside of the cabin is spacious and bright to improve the experience of the passengers and to facilitate the driving of the boarding bridge.
- Water proof aluminum slats for noise reduction for extended life
- Synchronized slat rotation system without chain/gear (maintenance free)
- Cabin rotation +90º/-35º made by electric motor
- Super soft bumper to avoid any damage to the aircraft fuselage
- Nr. 3 Proximity Sensors positioned inside the bumper and Nr. 1 aircraft detection ultrasound sensor
A Passenger Boarding Bridge is an enclosed, elevated mobile walkway which extends from an airport terminal gate to an aircraft door.
Yes, in fact there are many terms used around the world, like: Passenger Loading Bridge, Aerobridge, Airbridge, Jetbridge and Jetway, The abbreviation of Passenger Boarding Bridge is PBB.
An apron-drive Passenger Boarding Bridge starts with a Rotunda, fixed over a Rotunda Column, which is anchored into the ground. The Rotunda is the interface between the airport building (a fixed structure) and the mechanical bridge (a movable structure). Two or three Telescopic Tunnels are the next part of bridge. They are supported by the Rotunda on one side and the Elevation System on the other. The Elevation System comprises two parallel steel pillars or columns, assembled over a Traction System (also known as bogie) which contains motors and wheels. This system makes it possible for the Passenger Boarding Bridge to manoeuvre to and from the aircraft. Finally, at the end of the telescopic tunnels is the Cabin, which is the part of the Passenger Boarding Bridge that connects with the aircraft.
The first Passenger Boarding Bridges, as we know them today, were found in the USA. A single prototype, the “Aero-Gangplank”, was installed in 1958 at Chicago’s O’Hare International Airport. One year later, Pacific Iron and Steel Corporation installed the first fully operational “Jetways” at both San Francisco International Airport and Atlanta Airport. The first Passenger Boarding Bridge outside the USA was installed in 1961 at Amsterdam Schiphol Airport.
ADELTE received its first contract to design, manufacture and install a Passenger Boarding Bridge in 1984. The PBB was installed at Tenerife airport, on the Canary Islands.
Yes, there are various types of PBBs. The Apron Drive-type is the most commonly used worldwide. Additionally, there are also Nose Loader, T-loader, Commuter Bridge and the A-380 Apron Drive.
An Apron Drive-type Passenger Boarding Bridge usually reaches a height of five meters. However, the Apron Drive A380 Passenger Boarding Bridge can be elevated to reach a height of up to eight meters.
The weight of a Passenger Boarding Bridge is on average around 25 tons, although this weight varies depending on the number of tunnels, their length and the components installed.
The purchase price of a Passenger Boarding Bridge can vary depending on the type, functions and finishes that a client requires. PBBs can have two or three tunnels with glass or steel side panels, can be fixed or use a traction system, and finally can include a hydraulic or electro-mechanical elevation system. Furthermore, the airport location where the PBB will be installed also has an impact on its price.
In general Passenger Boarding Bridges are acquired by airport authorities to integrate them into their terminals as part of their infrastructure. However, airport operators and airlines also acquire and own Passenger Boarding Bridges.
Passenger Boarding Bridge Specifications
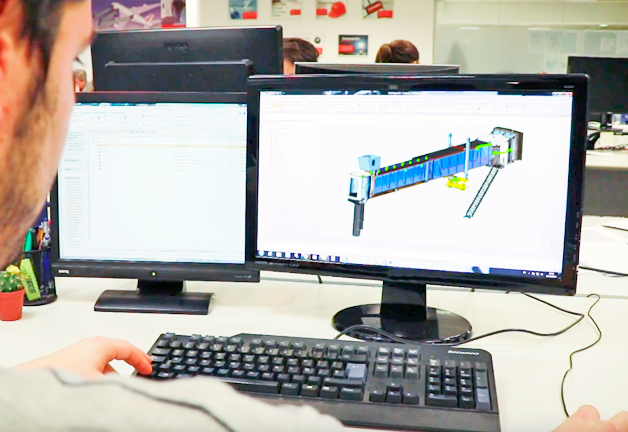
Our engineers will design and deliver a Boarding Bridge manufactured to your specific needs, choosing the right size configuration, the drive system, the elevation type (hydraulic or electro-mechanical), a two or three body configuration, the most efficient air conditioning system and other design features, such as glass or steel tunnels, increasing or decreasing telescope extension or GSE integration. The result is a highly durable Passenger Boarding Bridge capable of providing a long-lasting service at your airport.
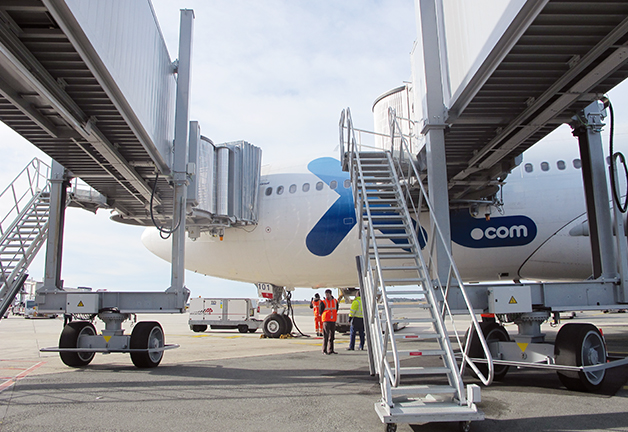
Elevation and travel systems are designed and engineered to offer maximum energy efficiency. The Passenger Boarding Bridge structure is prepared to receive Ground Support Equipment such as PCA and GPU which deliver preconditioned air and electricity to the stationed aircraft, dramatically reducing its energy consumption.
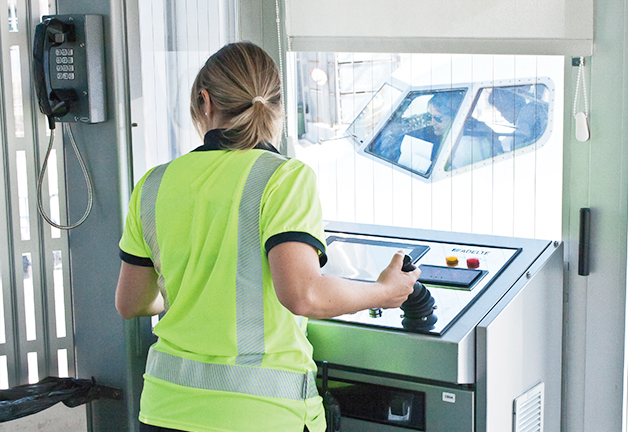
ADELTE’s Passenger Boarding Bridges are equipped with the latest Cabin and PLC technologies and offer a complete and reliable safety system. Multiple sensors, point-and-go technology and our fully automated docking system make docking operations simple and successful, preventing any risk for the aircraft or operator on the apron.
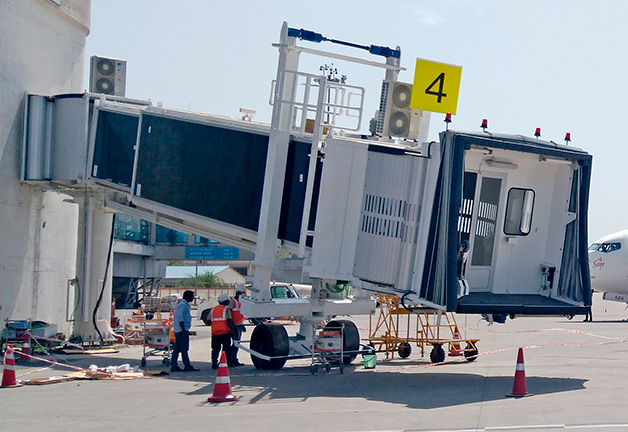
Maintenance is a key factor for keeping boarding bridges in optimum operating condition. Thanks to our unique direct access design, all major components can be reached easily to allow maintenance tasks to be carried out quickly.
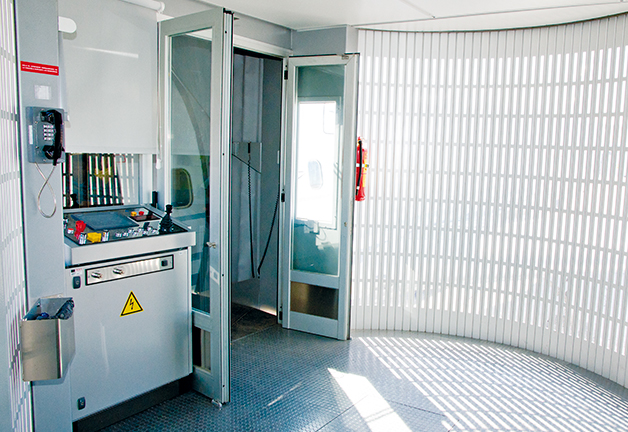
Our Passenger Boarding Bridges offer a stronger and more lightweight structure made of high quality steel which ensures the best protection against corrosion. All materials are tested and the manufacturing process is certified in order to guarantee excellent durability.
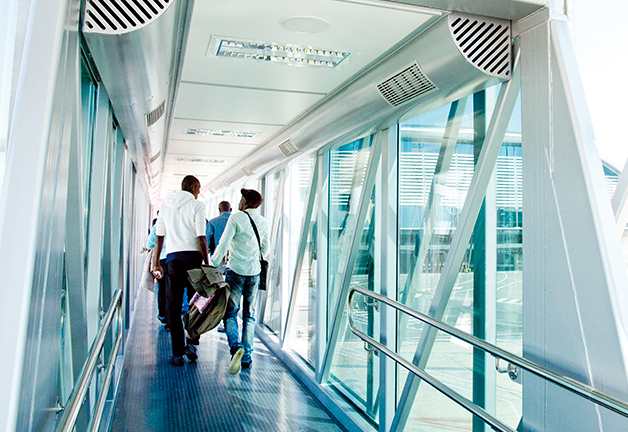
We strongly believe that the moment a passenger enters one of our advanced boarding bridges they begin their journey. Therefore, design and a successful technical conception are vital, incorporating aspects such as innovative use of natural lighting, significant thermal and acoustic insulation, non-slip flooring, efficient air-conditioning solutions and comfortable gradient, all of which make a qualitative difference to a passenger’s perception of the service provided by an airport or airline.
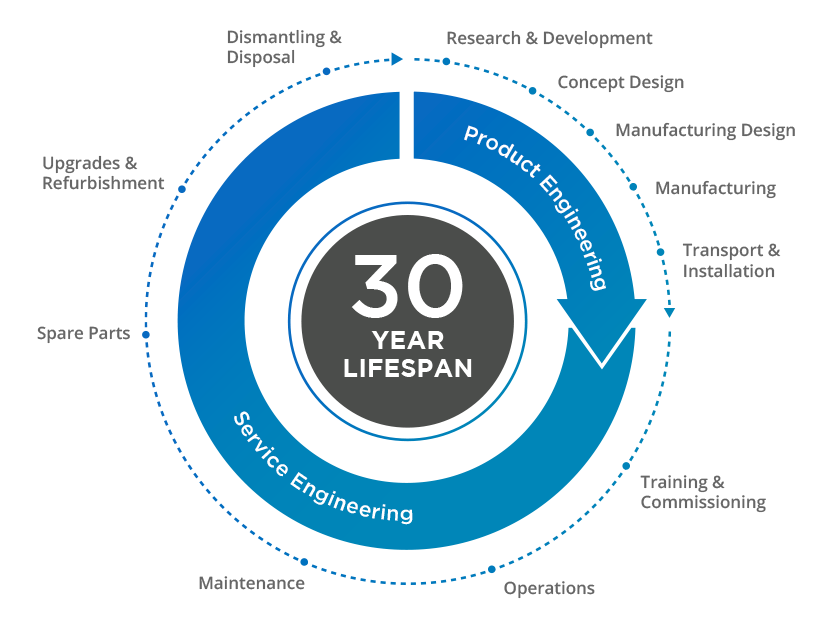